مهندسي سطح ، به عنوان دانشي براي تکميل و بهبود خواص سطح در گستره اي از فلزات ، پلاستيک ها، پليمرها و ساير مواد مهندسي جايگاه ويژه اي دارد و به همين دليل همواره شاهد نوآوري و ارتقا در روشهاي مهندسي سطح هستيم.به طور کلي با فرآيندهاي سطح ، خواص سطحي قطعات صنعتي را از لحاظ مقاومت سايشي و مقاومت خوردگي مي توان بالا برد.
خوردگي عبارت است از تخريب ناخواسته يک ماده در اثر واکنش آن با محيط اطرافش. در اين ميان فلزات قابليت هدايت الکتريکي زيادي دارند و فرآيند خوردگي در آنها از نوع الکتروشيميايي است. در حالي که براي مواد غير هادي ، از نوع شيميايي است و اصول شيمي فيزيکي درباره آنها مطرح مي شود.
امروزه اهميت خوردگي فلزات بيشتر از گذشته است چراکه استفاده از فلزات گسترش يافته است ، کاربردهاي ويژه نظير انرژي اتمي ، استفاده از فلزات نادر و گرانقيمت را طلب مي کند که جلوگيري از خوردگي آنها نيز اهميت ويژه اي دارد، خورندگي محيط بر اثر آلودگي آب و هوا افزايش يافته است که موجب افزايش خوردگي فلزات مي شود و در طراحي هاي جديد استفاده از سازه هاي سبکتر الزامي است و بنابراين همچون گذشته که سازه ها سنگين تر بود، نمي توان خوردگي را ناديده گرفت
در اين شرايط در کنار افزايش عمر مفيد قطعات ، امکان ساخت قطعات با مواد اوليه ارزان تر نيز ممکن مي شود. مهندسي سطح ، پهنه وسيعي از کاربردها از موارد تزئيني و در مصارف خانگي گرفته تا موارد فني و در مصارف صنعتي را شامل مي شود و تاثير مثبتي در انتخاب مواد، روش توليد، ملاحظات اقتصادي و نگهداري و تعميرات قطعات دارد.
در اين ميان پوشش کاري يکي از روشهاي مهندسي سطح و براي تکميل خواص سطحي قطعات يا تعمير و بازسازي آنهاست. روشهاي متفاوتي براي پوشش کاري با توجه به خواص مورد نياز پوشش و جنس مواد اصلي (پايه) و نيز محدوديت هاي فني وجود دارد. اما نکته مشترک در همه اين روشها، دستيابي به خواص بهينه تر و هزينه تمام شده کمتري با تغيير پارامترهاي موثر در هر روش است. به گفته مهندس عبدالخالق حسن زاده ، فارغ التحصيل کارشناسي ارشد دانشکده مهندسي معدن و متالورژي دانشگاه صنعتي اميرکبير يکي از مواردي که براي مقابله با آن ، از پوشش کاري سطوح کمک گرفته مي شود، خوردگي و اکسيداسيون سطح قطعات است.
حسن زاده مي افزايد: خوردگي ، عامل بخش عمده اي از شکست سازه هاي فلزي است و اهميت آن نه تنها از اين نظر است که شکست در بيشتر موارد ناگهاني است ، بلکه بيشتر به علت حضور و تاثير همه جانبه آن است.
پوششهايي از جنس روي
پوشش کاري روي با روشهاي متنوعي صورت مي گيرد و پوشش حاصل از هر کدام از اين روشها، ويژگي ها و مشخصات خود را دارند و پارامترهاي متفاوتي مانند دماي فرآيند، زمان فرآيند، آناليز شيميايي محلول يا پودر فرآيند و ساير عمليات جانبي ديگر مانند عمليات حرارتي ، عمليات مکانيکي و عمليات شيميايي تکميلي در کيفيت پوشش تاثير دارند. بنابراين با توجه به خواص مورد نياز و مطالعات اقتصادي و محدوديت هاي هر فرآيند، بايد روش مناسب را انتخاب کرد.
حسن زاده درباره مزايا و موارد استفاده روش نوين مي گويد: پوشش حاصل از روش نفوذي در حالت جامد داراي برتري هاي نسبي در مقايسه با ساير روشهاي ديگر است که از آن جمله مي توان به عدم آلايندگي محيط زيست ، مصرف کمتر انرژي ، سهولت فرايند پوشش کاري ، يکنواختي سطح پوشش ، امکان تشکيل پوششهاي رنگي ، امکان پوشش کاري مناسب شيارها، لبه هاي تيز و منافذ قطعات و بويژه عمر طولاني تر (نرخ خوردگي کمتر) پوشش اشاره کرد. ضمن آن که عمده ترين موارد کاربرد اين روش نوين ، پوشش دهي پيچ و مهره ها، واشرها، بست ها و قطعات داراي منافذ و سوراخ هاي ريز و کوچک در صنايع خودروسازي ، صنايع دريايي و زيردريايي ، قطعات کشاورزي و باغباني ، خطوط انتقال برق و تجهيزات ماهواره اي و مخابرات ، صنايع پتروشيمي و… است.
اين روش براي نخستين بار در دنيا، در سال 2000 ميلادي توسط يک تيم پژوهشي از دانشمندان روسي و به نام اسرائيل (رژيم اشغالگر قدس) تحت عنوان تجاري Distek ابداع و ثبت شد.
به اين ترتيب تمامي صنايع استفاده کننده از اين روش پس از خريد تکنولوژي از اين شرکت اسرائيلي براي تامين پودر مورد نياز و ساير خدمات فني ، به نمايندگي هاي انحصاري اين شرکت در چند کشور وابسته هستند.
به همين دليل هم تاکنون از اين روش در کشور ايران استفاده نشده است و پس از مطالعات و پژوهش هاي انجام شده در اين زمينه و دستيابي به ترکيب پودر مناسب که داراي قيمت تمام شده پائين تري نسبت به پودر مشابه است ، امکان استفاده صنعتي از اين روش بدون نياز به خريد تکنولوژي و وابستگي هاي بعدي در داخل کشور به وجود آمده است.
مزاياي نفوذ در حالت جامد
حسن زاده با اشاره به آزمايش هاي انجام شده در اين پژوهش ، مي افزايد: نرخ خوردگي در آهن پوشش داده شده با روش غوطه وري گرم گالوانيزه به طور متوسط 350 ميکرون است در حالي که در نمونه به دست آمده اين ميزان به 15 ميکرون رسيده است. در اين طرح پوشش هايي با ضخامت 60 تا 95 ميکرون ايجاد شد و نتايج هم با استفاده از ميکروسکوپ نوري ، ميکروسکوپ روبشي (STM) و همچنين با کمک اشعه ايکس (XRD) بررسي و صحت سنجي شد. درواقع به کمک اين روش با توجه به ضعف فولاد در برابر خوردگي ، فلز روي که در سطح فلز قرار مي گيرد، خورده شده و محصولات خوردگي آن با تشکيل لايه اي متراکم و چسبنده نفوذ خوردگي به فولاد را بسيار کند مي کنند. به گفته حسن زاده در اين شيوه که نخستين بار در سال 2000 ميلادي ثبت شده پودر روي مخلوط با چند ماده کمکي ديگر، در درجه حرارت معين و بدون نياز به ذوب شدن در سطوح فولاد نفوذ مي کند و پوشش محافظ تشکيل مي شود.
پيچيدگي اين روش در تعيين ميزان مواد کمکي ، حرارت مورد نياز و سرعت چرخش قطعات براي پوشش دهي به شمار مي رود. در اين تحقيق عمليات پوشش دهي روي بر روي نمونه هايي از جنس فولاد ساده کربني انجام گرفت.
از پودر روي هم به عنوان منبع تامين کننده روي ، استفاده شده است.
بطورکلي در پوشش دهي به حالت چرخشي ، نمونه به همراه مخلوط پودر در يک محفظه استوانه اي فولادي ريخته مي شود.
در واقع اين محفظه توسط يک موتور گرداننده با دور چرخش قابل کنترل در درون يک کوره مقاومتي استوانه اي با سرعت معين چرخانده مي شود. پس از تعيين ترکيب بهينه پودر با توجه به نتايج آزمون پتانسيو استات و مطالعات ريز ساختاري ، در دما و زمان ثابت و سرعت چرخش معين ، به منظور دستيابي به شرايط مناسبي از متغيرهاي موثر در کيفيت پوشش ، فرآيند پوشش دهي صورت مي گيرد؛ سپس پس از تعيين دماي بهينه ، عمليات در مدت زمان هاي مختلف و پس از آن با سرعت چرخش هاي متفاوت انجام مي گيرد. به منظور بررسي امکان پذيري انجام فرآيند پوشش دهي در حالت ساده تر، آزمايش هايي در حالت ثابت انجام مي شود. در اين روش ، ابتدا نمونه هاي آماده سازي شده به همراه پودر فرآيند در جعبه اي از جنس فولاد نسوز قرار مي گيرند و روي آنها با يک ورقه فولادي پوشانده مي شود و در نهايت به منظور جلوگيري از اکسيد شدن پودر با اتمسفر کوره ، سطوح جعبه با مخلوط گل و سيمان نسوز پوشانده مي شود.
در واقع در اين روش تشکيل لايه هاي آلياژي آهن – روي باعث کاهش نرخ خوردگي پوشش ايجاد شده مي شود، فاز زتا در آب بندي کردن ترک هاي موجود در لايه مياني (فاز دلتا) و در نتيجه افزايش مقاومت به خوردگي پوشش تاثير مثبت دارد، استفاده از ترکيب بهينه پودر فرآيند باعث افزايش مقاومت به خوردگي پوشش مي شود، استفاده از ترکيب بهينه پودر فرآيند باعث کنترل ضخامت فاز ترد و شکننده زتا مي شود و دستيابي به لايه اي متشکل از سه فاز گاما، دلتا و زتا با روش پوشش دهي نفوذ در حالت جامد به حالت چرخشي امکانپذير است.
پوشش دهی به روش اسپری حرارتی و انواع آن
اسپری حرارتی
به مجموعه ای از فرآیند های پوشش دهی گویند که در آنه ماده پوشان توسط گرمای یک منبع حرارتی به صورت ذوب یا خمیری در آمده و سپس توسط یک گاز با فشار زیاد به شکل قطرات ریز بر روی زمینه قرار می گیرد در این فرآیندها در واقع گرمای موجود برای ذوب کردن ماده پوشان صرف گرم نمودن گاز نیز می شود که با گرم شدن آن فشار گاز نیز افزایش می یابد و با سرعت زیادی ماده پوشان را به صورت اتمیزه بر روی قطعه می نشاند
تمام فرآیند های اسپری حرارتی دارا اجزائی از جمله منبع تغذیه ماده پوشان –مخازن گاز –تفنگ اسپری و سیستم کنترل می باشد
این فرآیند در سال 1910 در سوئیس ابداع شد نوع تغذیه مواد پوشش در این روش به دو صورت سیمی و پودری می باشد در نوع سیمی که ماده پوشان به صورت سیم یا مفتول می باشد از پشت تفنگ وارد شده و با گرم شدن به صورت قطرات مذاب در آمده و در اثر فشار و سرعت زیاد گاز به سمت قطعه پاشیده می شود در روش اسپری حرارتی با تغذیه پودری ماده پوشان به صورت پودر همرا با یک گاز حامل وارد شعله تفنگ می شود در واقع با حرکت سریع گازهای داغ شعله از جلوی دهانه تغذیه کننده پودر حالت خلا در این قسمت ایجاد می گردد و پودر همرا با گاز حامل به درون شعله کشیده می شود این ذرات نیز پس از ذوب شدن یا خمیری شدن به سطح قطع برخورد می نماید و به آن می چسبد
یکی دیگر از روش های تغذیه روش پیستوله ای می باشد در این روش ماده پوشان به صورت مذاب درآمده و در مخزنی نگه داری می شود و با عبور سریع جریان هوا از جلوی روزنه مخزن مذاب به بیرون کشیده شده و به صورت پودر بر روی زیر لایه قرار می گیرد البته این روش امروزه کمتر استفاده می شود
در اسپری حرارتی امکان استفاده از دو یا چند مده نیز وجود دارد بنابراین در مواردی که نیاز به پاشش مواد مرکب و یا مخلوط وجود داشته باشد می توان از دو یا چند مخزن و یا چند سیم از مواد پوشان استفاده می شود و یا می توان پودر مواد را با هم مخلوط کرد و پاشش را انجام داد در پاشش مواد مخلوط نیز امکان ترکیب آنها با یکدیگر وجود دارد به عنوان مثال تولید پوشش NiAL می توان با اسپری پودر نیکل و AL در شرایط مخصوص انتظار داشت که پوشش NiAL بدست آید در عین حال امکان اپری پودر ترکیب NiAL نیز به صورت مستقیم وجود دارد به این روش که در حین پاشش مواد پوشان دو ماده با هم ترکیب شوند و پوشش جدیدی را ایجاد ماید ترمو اسپری گفته می شود در این فرآیند اغلب ترکیب شدن دو ماده پوشان همراه با آاد سازی حرارت می باشد و این حرارت اضافی موجب بهتر شدن خواص پوشش و کیفیت آن می گردد امروزه از این روش در صنایع پیشرفته هوافضا استفاده می شود
انواع اتصال پوشش به زیرلایه
در اثر برخورد ذرات ریز ماده پوشان به سطح قطعه این ذرات اتصال هایی را با زیر لایه بر قرار می کنند و در واقع می توان نوع اتصال پوشش به زیر لایه را در تمام انواع اسپری حرارتی به س نوع تقسم کرد
1- اتصال مکانیکی : یعنی درگیر کردن ذرات در بین مشخصه های سطحی زیرلایه.
2- ایجاد ترکیب بین زیر لایه و پوشش که در واقع به علت نفوذ و تشکیل آلیاژ ایجاد می گردد.
3- اتصال ضعیف واندوالس بین ذرات و سطح که حاصل از جاذبه اتمی می باشد
انواع اسپری حرارتی
(FLAME SPRAY( 1- اسپری شعله ای :
در این روش که ساده ترین فرآیند اسپری حرارتی می باشد حرارت لازم برای ذوب نمودن مواد پوشان توسط سوختن یک گاز (استیلن ) تامین می گردد این روش یرای پوشش دهی فلزات و بعضی از موادی که نقطه ذوب بالایی ندارند استفاده می گردد در عین حال مقداری اکسید در پوشش های فلزی و تخلخل در همه پوشش های تولید شده به این روش زیاد می باشد و در نتیجه از این روش برای ایجاد پوشش های با کیفیت متوسط و پوشش هایی که نیاز به تخلخل دارند مانند یاتاقان ها استفاده می شود ولی در واقع بهترین مزیت آنها ارزان بودن است و نیاز به کنترل زیادی ندارد.
در این روش گاز استیلن و اکسیژن از درون مجاری مخصوص به سر تفنگ رسیده و در این محل شعله ور می گردد مواد پوشان نیز به درون شعله تغذیه شده و پس از ذوب شدن بر روی زیر لایه قرار می گیرد .
) DETONATION GUN (DG 2- روش اسپری با تفنگ انفجاری
این روش از روش های جدید است که جهت ایجاد پوشش هایی با کیفیت بسیار بالا به کار می رود در این روش مخلوط اکسیژن و استیلن با نسبت خاصی وارد لوله تفنگ می گردد که پس از انفجار حجم گاز زیاد شده و با سرعت زیادی از تفنگ خارج می شود در این حال با تغذیه مواد پوشان می توان پوششی بسیار متراکم و با کیفیت را به دست آورد در این روش انفجار به طور مداوم وجود ندارد بلکه توسط جرقه هایی و در زمان های خاصی احتراق صورت می گیرد این روش سرعت پوشش دهی پایینی دارد و صدای آن بسیار زیاد است به همین دلیل از این روش در موارد خاصی که نیاز به پوشش هایی باکیفیت بالا باشد استفاده می شود از این روش به طور معمول برای ایجاد پوشش های سرامیکی جهت کار در دمای بالا استفاده می شود .
3 – روش پوشش دهی با قوس الکتریکی
در این روش منبع حرارتی با ایجاد قوس الکتریکی بین دو سیم از جنس ماده پوشان تامین می گردد و به عبارت دیگر این روش مخصوص پوشش دادن مواد رسانا می باشد قوس بین دو سیم از جنس ماده پوشان ایجاد می گردد و آنه را ذوب اتمیزه می کند سپس با استفاده از یک جریان گاز ذرات بر روی زیر لایه قرار می گیرند این روش سرعت پوشش ذهی بالایی دارد و نسبتا ارزان می باشد و نیاز به گازهای گران قیمت ندارد این پوشش ها دارای چسبندگی و پیوستگی خوبی هستند
(HVOF( 4– روش اسپری سوخت و اکسیژن با سرعت زیاد
این روش یکی از پیشرفته ترین روش های اسپری است که در آن سوخت واکسیژن با نسبت خاصی باهم مخلوط شده و پس از احتراق با فشار و سرعت زیادی از دهانه تفنگ خارج می شوند ، سرعت گاز به بالای سرعت صوت می رسد در این روش دمای ماده پوشش بالا نمی رود و ذرات نیمه مذاب ماده پوشان در اثر برخورد شدید با سطح زیر لایه انرژی لازم برای ذوب شدن را بدست می آورند که در نتیجه پس از برخورد بر روی سطح به صورت مذاب در آمده و به زیر لایه می چسبند . این روش کیفیت بسیار خوبی دارد و مقدار اکسید وتخلخل کمتری نیز دارد
گازهای مورد استفاده این روش پروپن – پروپیلن یا هیدروژن می باشند و این روش در تولید قطعات توربین های جت کاربرد زیادی دارد.
5 – روش اسپری پلاسمایی:
این روش از پر استفاده ترین روش ها در صنعت می باشد که علت آن ارزان بودن سرعت بالای پوششمی باشد در واقع پلاسما اسپری روش مناسب برای ایجاد پوشش های دیر گداز و مقاوم به سایش و خوردگی با کیفیتی مناسب می باشد و به عنوان مثال از آن برای پوشش دهی انواع سرامیک ها بر روی غلطک ها استفاده می گردد و عملکرد آن به این صورت است که تفنگ پلاسمایی متشکل از یک آند مسی به صورت آبگرد و یک کاتد تنگستنی و نازل مواد پوشان می باشد طرز کار به این صورت است که ابتدا اختلاف پتانسیلی بین آند و کاتد برقرار شده و سپس گاز بین آند و کاتد یونیزه شده و با برقراری جریان برق گاز به شذت گرم می گردد و حجم آن اضافه می شود در این حال گاز با فشار از دهانه تفنگ خارج شده که اگر ماده پوشان به صورت پودر باشد ذرات ماده پوشان در دهانه خروجی تفنگ به درون شعله تغذیه می گردد و اگر به صورت سیم باشد از عقب تفنگ و به کمک چند غلطک وارد قسمت پلاسما می گردد پی از ورود ذرات به درون شعله پلاسما این ذرات بر حسب اندازه ای که دارند ذوب و یا نیمه مذاب می شوند و با سرعت بر روی سطح زیر لایه برخورد می کنند تا پوشش تشکیل شود .
شرایط ایده آل شرایطی است که دمای ذرات بر روی سطح برابر نقطه ذوب آنها باشد.
6 – اسپری حرارتی تحت خلا و گاز خنثی
در اسپری حرارتی عاملی که در افت کیفیت پوشش دهی بسیار نقش دارد اتمسفر محیط است به طوری که پس از خروج ذرات همراه با شعله از دهانه تفنگ گازها نحیطی وارد شعله گردیده و علاوه بر کم کردن دما و سرعت شعله و ذرات باعث ایجاد ترکیب با ذرات مذاب پوشش می گردد در چنین شرایطی حذف گاز های محیط بسیار مفید خواهد بود و در عین حال کیفیت پوشش بالا می رود که جهت این کار از دو روش استفاده می کنند
الف – پوشش دهی تحت اتمسفر گاز خنثی
ب – پوشش دهی در فشار پایین (خلاء)
در هر دو این روش ها پوشش دهی در محفظه بسته انجام می شود بنابراین در اندازه قطعات محدودیت داریم
نظرات شما عزیزان:
محمد رضا بکرانی 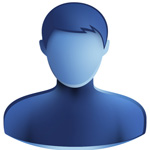
ساعت18:17---4 فروردين 1392
با سلام- لطفا اگر مقاله یا مطلبی در مورد پوشش دهی فلزات به روش انفجاری در اختیار دارید برای من بفرستید
با تشکر
|